Lexicon
An evaluation of material use within exterior restoration projects requires defining common terminologies, as well as distinguishing among terms used as synonyms that may not necessarily mean the same thing.
“Substitute” vs “Alternative”
Used interchangeably within the industry, these terms have come to be synonymous. Both refer to a material, product, or system used in place of another. This could involve replacement of select units, comprehensive reconstruction of entire areas and, in some cases, building additions, especially in historic districts. Note that substitutes do not necessarily have to involve more contemporary synthetic materials. Instead, they might also include traditional materials that are more suitable to the application than the original material.
“Existing” vs “Original” vs “Historic”
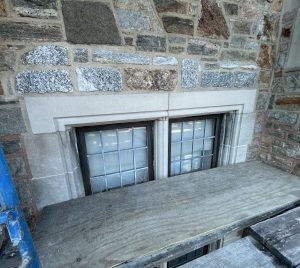
Cast stone stands in for limestone at this historic window header.
Although there are instances where all mean the same thing, these terms are not inherently interchangeable. Existing material, which is currently present, may or may not be the same as the original material, used when the building was constructed. Historic, a more ambiguous term, could imply there is cultural or architectural value to the original building or material, or it might refer to the fact the original construction dated to a certain era or is no longer employed in contemporary practice. These are important distinctions, because replacement always involves existing materials but not necessarily original or historic ones, as the latter two might have already been replaced in a prior project.
“Traditional”
If some original material has been replaced with different materials, the question of which should be matched must also be answered. It is important to note that historic does not necessarily mean traditional (e.g. stone and wood), as it could reference industrial materials used in 20th century Modernist-style buildings. Furthermore, traditional construction does not necessarily mean the structure is old. The Basilica of Sagrada Familia in Barcelona, Spain, designed by Antoni Gaudí, has been under construction for 140 years, and new stone masonry is still being laid per the architect’s original plans. Moreover, thousands of vernacular structures around the world are still built using traditional materials.
“In-Kind”
Matching in-kind is often the desired approach when replacing materials, but what in-kind means can be unclear. Does it mean matching material that is original, or, if different, existing? Is it matching general appearance, like size, shape, color, and texture, or physical properties, as per officially recognized standards? Must the material come from the original source, such as a particular quarry or shop, and does it need to be fabricated the same way?
Even where in-kind material is specified, it is critical to understand that not all stone, wood, or metal is created equal. Sourcing, extraction, processing, and classification impact a material’s quality. Even if replacement material has the same origins, adjacent existing material may have weathered over time, so it may be impossible to truly match its properties and appearance. These considerations demonstrate the perils of over-reliance on the phrase in-kind without detailed criteria for its project-related meaning and thorough technical specifications that clarify these ambiguities.
“Preservation” vs “Rehabilitation” vs “Restoration” vs “Reconstruction”
Other important terminologies to consider include those officially recognized within The Secretary of the Interior’s Standards for the Treatment of Historic Properties, established under the National Historic Preservation Act (NHPA). This document defines four different approaches for treating historic properties:
- Preservation focuses on the maintenance and repair of existing historic materials and retention of a property’s form as it has evolved over time.
- Rehabilitation acknowledges the need to alter or add to a historic property to meet continuing or changing uses while retaining the property’s historic character.
- Restoration depicts a property at a particular period of time in its history, while removing evidence of other periods.
- Reconstruction re-creates vanished or non-surviving portions of a property for interpretive purposes.
(National Park Service, “Four Approaches to the Treatment of Historic Properties”)
Many projects involve aspects of more than one of these approaches, and the use of substitutes could fall under any of them. However, substitutes are more likely entertained when performing the three latter approaches.